不锈钢管道因其优异的耐腐蚀性、高强度和长寿命,广泛应用于石油化工、食品饮料、医药制造等领域。然而,表面质量问题(如划痕、氧化皮、色差、焊缝缺陷等)仍是制约产品附加值与客户满意度的关键痛点。据统计,因表面缺陷导致的退货率占不锈钢管道质量问题的60%以上。本文将从原料选择、生产工艺、设备升级及质量检测四大维度,系统阐述如何从源头构建表面质量防控体系,助力企业提升产品竞争力。
一、原料把控:选对材质是基础
钢种匹配应用场景
不同牌号的不锈钢(如304、316L、2205双相钢)化学成分差异显著,需根据介质特性(如氯离子含量、温度、压力)选择合适材质。例如,沿海地区供水管道建议采用316L以抵抗氯离子腐蚀,避免表面点蚀引发的质量隐患。
原料表面预处理
原料卷材或板坯表面若存在油污、锈蚀或划伤,会在后续加工中放大缺陷。企业应引入自动化清洗线,通过碱洗、酸洗、喷砂等工艺去除表面杂质,同时采用激光扫描检测原料表面平整度,剔除不合格材料。
供应商分级管理
建立原料供应商白名单制度,定期抽检其熔炼工艺、成分均匀性及表面缺陷率。例如,某头部企业通过与钢厂联合开发“管道专用钢”,将原料表面缺陷率从3%降至0.5%,从源头减少了后续处理成本。
二、生产工艺优化:精细化控制是关键
成型环节:减少机械损伤
冷轧/冷拔工艺:采用多道次小变形量轧制,避免单次压下量过大导致表面橘皮纹;冷拔后需立即进行脱脂处理,防止润滑剂残留引发氧化。
弯管工艺:使用中频感应加热弯管机,通过精准控制加热温度(850-950℃)和弯曲半径,避免管壁减薄或表面褶皱。某企业通过优化弯管模具设计,将焊缝与弯曲轴线的夹角控制在45°以上,显著降低了弯管区裂纹风险。
焊接环节:消除焊缝缺陷
自动化焊接技术:推广等离子焊接、激光焊接等高精度工艺,替代传统手工氩弧焊,减少焊缝余高(建议≤0.5mm)和咬边深度(≤0.1mm)。
焊后处理:采用机械抛光+电解抛光组合工艺,先通过砂带机去除焊缝飞溅,再利用电解液(如磷酸+硫酸混合液)进行表面整平,使焊缝区与母材光泽度差≤10%。
热处理环节:控制氧化与脱碳
固溶处理时需快速升温至1050-1150℃,并严格控制保温时间(按管壁厚度1.5分钟/mm计算),随后水淬冷却以防止碳化物析出。某企业通过在退火炉内充入氮气保护,将管道表面氧化皮厚度从15μm降至5μm以下,减少了后续酸洗损耗。
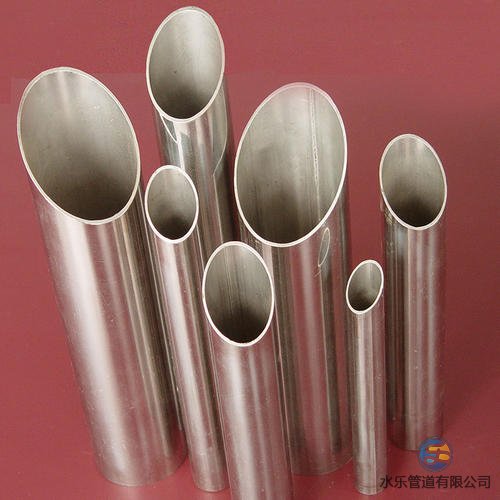
三、设备升级:智能化赋能质量提升
高精度加工设备
引入六轴数控机床进行管端倒角加工,通过编程控制切削深度(建议≤0.2mm)和表面粗糙度(Ra≤0.8μm),避免手工打磨导致的局部过热变色。
在线检测系统
表面缺陷检测仪:采用CCD相机+AI图像识别技术,实时监测管道表面的划痕、孔洞等缺陷,检测速度可达30米/分钟,准确率超99%。
内窥镜探伤:对弯头、三通等异形件内部进行可视化检查,及时发现裂纹或焊瘤,替代传统射线检测的耗时与辐射风险。
清洁生产环境
建设无尘车间(洁净度等级ISO Class 7以上),配备空气净化系统和防静电地板,减少加工过程中灰尘附着导致的表面瑕疵。某企业通过升级车间环境,将管道表面清洁度从Ra3.2μm提升至Ra1.6μm,满足半导体行业严苛要求。
四、质量检测与追溯:闭环管理防风险
全流程数据记录
利用MES系统记录每根管道的原料批次、工艺参数、检测结果等信息,生成唯一二维码标识,实现质量追溯至具体工位和操作人员。
破坏性抽检与模拟测试
盐雾试验:按ASTM B117标准进行720小时中性盐雾测试,验证表面钝化膜耐蚀性。
压力循环测试:对管道施加1.5倍额定压力的交变载荷,检测焊缝区是否出现泄漏或表面起泡。
客户反馈驱动持续改进
建立质量问题快速响应机制,对客户投诉的表面缺陷进行根因分析(如通过SEM扫描电镜定位裂纹源),并反向优化生产工艺参数。例如,某企业通过分析客户退货管道的焊缝金相组织,发现热输入过量导致晶粒粗化,随后调整焊接电流,将焊缝冲击韧性提升20%。
结语:源头防控比事后修复更高效
不锈钢管道表面质量问题的解决,需从原料选择、工艺设计、设备投入到检测追溯形成闭环管控。企业通过引入智能化技术(如AI检测、数字孪生)和精益生产理念(如单件流、防错设计),可显著降低质量成本(通常占销售额的5%-15%)。在高端制造领域,表面质量已成为客户选择供应商的核心指标之一,唯有从源头筑牢质量防线,方能在激烈的市场竞争中脱颖而出。